Качество пайки радиоэлементов на печатных платах – это краеугольный камень надежности любого электронного устройства. Хоть пайка и является самым слабым звеном в цепочке надежности, без нее невозможно создать практически ни одно радиоэлектронное устройство.
Влияние на качество пайки
Существует ряд факторов, которые напрямую влияют на качество пайки и, соответственно, на надежность электроники:
1. Подготовка поверхности вывода и лужение на заводе-изготовителе. Завод-изготовитель, как правило, уже позаботился о качественной подготовке выводов радиоэлементов. Однако, даже в этом случае, важно проверить качество лужения. Лужение – это процесс нанесения тонкого слоя припоя на поверхность вывода, что обеспечивает лучшее смачивание и прочное соединение при пайке. Если лужение выглядит некачественным – неравномерным, шероховатым или имеющим видимые дефекты, необходимо зачистить выводы абразивным материалом, например, наждачной бумагой, и произвести повторное лужение. При этом важно соблюдать правила пайки, указанные в технической документации для конкретного радиоэлемента, чтобы избежать его перегрева.
2. Качество лужения точек пайки на печатной плате. Лужение точек пайки на печатной плате – это залог прочного соединения между компонентами и платой. Качество лужения зависит от выбранного метода:
– Погружная пайка: Печатная плата погружается в ванну с расплавленным припоем.
– Волновая пайка: Платы пропускают через волну расплавленного припоя.
– Ручная пайка: Припой наносится на контактные площадки паяльником. Качество лужения в каждой точке пайки должно быть одинаковым, без неровностей, воздушных пузырьков и неполного смачивания.
3. Качество флюса. Флюс – это специальное вещество, которое удаляет окислы с поверхности металла и обеспечивает лучшее смачивание припоем. Существует множество видов флюсов, но основные классификации – по типу активности (активные, слабоактивные) и по составу (жидкие, пастообразные, твердые). После пайки флюс должен удаляться, особенно на платах, где используются полевые транзисторы на входе, так как его остатки могут вызывать токи утечки, что может привести к нестабильности работы устройства.
4. Качество припоя. Качество припоя определяется его составом и температурой плавления. В зависимости от типа припоя, его температура плавления может варьироваться от 180 до 300 °C.
5. Растекаемость припоя. Растекаемость припоя – это способность расплавленного припоя свободно растекаться по поверхности, обеспечивая прочное соединение. Эта характеристика зависит от состава припоя.
6. Отверстия в плате. И, наконец, важно обратить внимание на отверстия в печатной плате, через которые проходят выводы радиоэлементов.
– Диаметр отверстия: должен соответствовать диаметру вывода компонента, чтобы избежать механических напряжений и деформации платы.
– Качество обработки: края отверстия должны быть гладкими, без заусенцев, которые могут повредить изоляцию вывода и привести к короткому замыканию.
– Положение отверстия: отверстия должны быть точно расположены относительно контактных площадок, чтобы исключить несоосность вывода и площадки, что может ухудшить контакт.
Качество пайки – один из ключевых факторов, определяющих надежность работы электронного устройства. Важно соблюдать все этапы подготовки к пайке, правильно выбирать материалы, и тщательно контролировать процесс пайки. Только в этом случае можно гарантировать надежность работы электронного устройства в течение длительного времени.
Как наличие отверстий в печатной плате может сказаться на качестве пайки выводов? Этот вопрос вызывает много споров, однако я постараюсь детально объяснить несколько аспектов, которые влияют на этот процесс.
Поскольку мы говорим о производстве печатных плат вручную или в полукустарных условиях, опустим вопрос металлизации отверстий. Этот процесс требует сложного оборудования для сверления, использующего высокие скорости и твердосплавные сверла.
Первым шагом к металлизации могли бы послужить пустотелые пистонные или трубчатые стойки, но, к сожалению, этот метод подходит лишь для объемных компонентов.
Теперь давайте подробнее обсудим, каким образом отверстия в плате могут повлиять на надежность и прочность соединений.
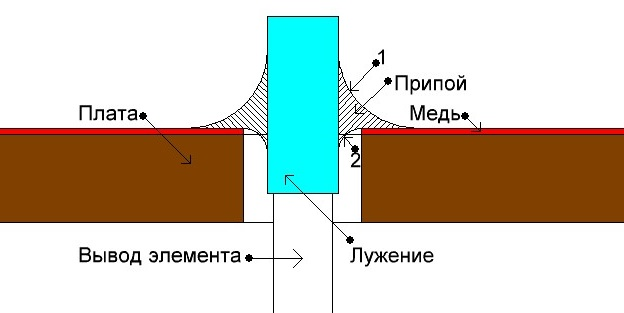
На представленном сечении платы можно увидеть припаянный вывод. Особое внимание следует уделить галтели 1, размеры которой могут варьироваться от небольших до больших в зависимости от объема припоя, используемого при пайке. Что касается галтели 2, ее параметры зависят от различных факторов: соотношения диаметров отверстия и вывода, уровня залуженности вывода, а также от залуженности и шероховатости края медной площадки. Как видно на изображении, минимальное расстояние между галтелями влияет на механическую прочность соединения. Таким образом, чем меньше разница между диаметрами отверстия и вывода, тем более надежным будет соединение. Теперь рассмотрим второй аспект: каким образом залуженность вывода влияет на прочность соединения. Более детально это касается конкретной зоны залуженности.
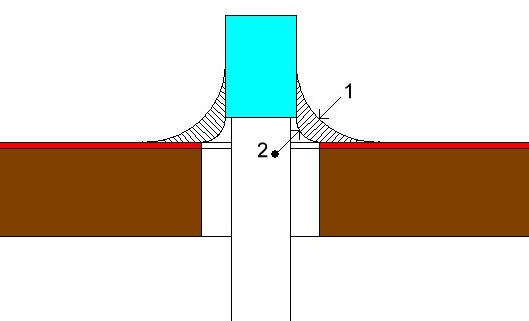
Как показывают данные на иллюстрации, залуживание произошло только в начальной части, и в соединении возникли узкие кольцевые области между галтелью 1 и галтелью 2. В то время как нижняя зона, обладая большим диаметром, имеет приемлемую прочность, верхнее кольцо будет значительно менее крепким!
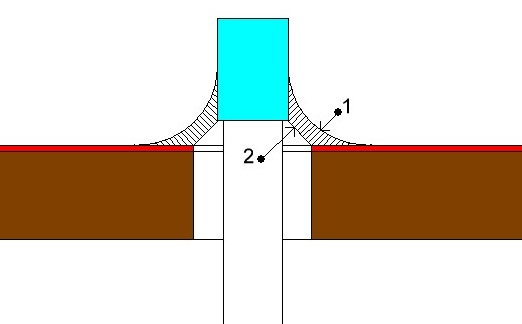
В данном месте представлен случай, когда галтель 2 была выпрямлена, что привело к снижению прочности соединения. Кроме того, к недостаточной прочности добавился важный аспект – возрастание переходного сопротивления пайки. Это означает, что если вывод подвергается значительным токам, пайка будет нагреваться, что может привести к негативным последствиям…
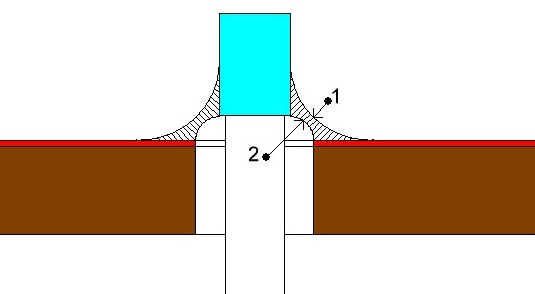
На этом изображении представлен наиболее неблагоприятный вариант (не исключаю, что может быть еще хуже!). В этом случае галтели ориентированы друг на друга, и даже на первый взгляд привлекательная пайка может привести к неисправности всего через несколько часов эксплуатации.
Из вышесказанного можно сделать вывод, что если деталь обладает значительным весом и вибрирует в процессе работы, то припой начнет трескаться, и как только трещина станет кольцевой, появится искрение. Сначала оно будет малозаметным, но в работе устройства возникнут сбои, а когда «прогар» станет серьезным, это повлечет за собой отказ других компонентов.
Встает вопрос: откуда же берется вибрация, если устройство стоит на столе?
Все очень просто! Импульсные трансформаторы излучают вибрации постоянно, просто мы их не слышим! Это неприятное явление практически невозможно устранить. Даже два проводника длиной в несколько миллиметров, находящиеся близко друг к другу и по которым течет ток, будут взаимодействовать — притягиваться или отталкиваться. Хотя это небольшая вибрация, в сочетании с частотой и длительным воздействием она уже даст свои негативные последствия. Учитывая, что импульсный трансформатор в блоке питания может выдавать 20 Ампер по каждому из напряжений, представьте, с каким усилием вибрирует вся схема.
Таким образом, при ремонте блоков с импульсными трансформаторами следует в первую очередь проверить соединения именно вибрирующих компонентов. Пайка — самый уязвимый элемент схемы.
Спасибо за внимание! Надеюсь, мои советы будут полезны не только новичкам. Желаю успехов в творчестве и ремонте! Помните, что все дело в пайке!