В данной статье рассматривается процесс самостоятельного производства печатных плат с высоким уровнем детализации. Указывается, что создание качественного фотошаблона с применением лазерного принтера, а также внедрение современных светочувствительных материалов и новых источников ультрафиолетового излучения вместо традиционных методов, значительно сокращает время и затраты на изготовление плат. Применение данной технологии позволяет разработчикам электронных устройств на актуальной элементной базе значительно ускорить процесс разработки и снизить его стоимость за счет оперативности и значительного удешевления процессов производства печатных плат.
Первая часть и вторая часть статьи.
Запайка деталей
Перед началом распайки компонентов на подготовленной плате её следует сначала облудить, а распайка компонентов — это следующий этап. Однако прежде чем перейти к описанию этих процедур, важно упомянуть о необходимых инструментах и добавочных элементах.
Сначала рассмотрим паяльники, которые были использованы автором. Для работы с самыми мелкими пассивными компонентами (такими как резисторы, конденсаторы, индуктивности в корпусах 0603), а также для микросхем с поверхностным монтажом в корпусах SSOP, QFN, с небольшим шагом (до 0,4 мм), и активными компонентами в корпусах SC70, SOT23, автор применял микропаяльник Ersa minor-S (6 В, 5 Вт) – см. рис. 36.

Тем не менее, данный паяльник требует некоторых улучшений. Проблема заключается в том, что «вечное» жало сделано из прочного и теплопроводного сплава, но этот материал имеет ощутимый недостаток: припой плохо прилипает к нему. В отличие от этого, медь, из которой изготавливают стандартные жала, отлично обеспечивает адгезию припоя, что делает её предпочтительной для использования. Рекомендуется заменить «вечное» жало на медное. Для этого нужно извлечь старое жало и создать новое из медного провода диаметром 1 мм, заменив им неэффективный элемент. Хотя этот процесс требует усилий, результат обеспечит более надежную и удобную пайку. Но это еще не все. Нагревательный элемент располагается не в самом конце ручки, а на 2–3 см выше, что предотвращает перегрев ручки и возможные ожоги. Однако такая конструкция создает длинный и гибкий консольный элемент, который пружинит. Чтобы уменьшить длину консоли и повысить её жесткость, рекомендуется использовать фторопластовые кембрики и наконечники, а также кольцо, изготовленное из пробкового дерева, что обеспечит необходимую поддержку.
Для создания пробкового кольца в пробке выполняется отверстие, ориентированное вдоль. Затем на винт устанавливается пробка, которая фиксируется с помощью двух шайб и гайки. После этого винт с пробкой помещается в патрон обычной ручной дрели. Далее включается дрель, устанавливается высокая скорость, и с помощью грубой, а потом более мелкой наждачной бумаги пробковое кольцо обрабатывается до необходимой формы. Консоль значительно укорачивается, жало паяльника фиксируется более надежно, что облегчает его позиционирование. Наличие термоизоляционных материалов, таких как фторопласт и пробка, позволяет удобно держать паяльник, не опасаясь ожогов, так как пробка остается холодной на ощупь.
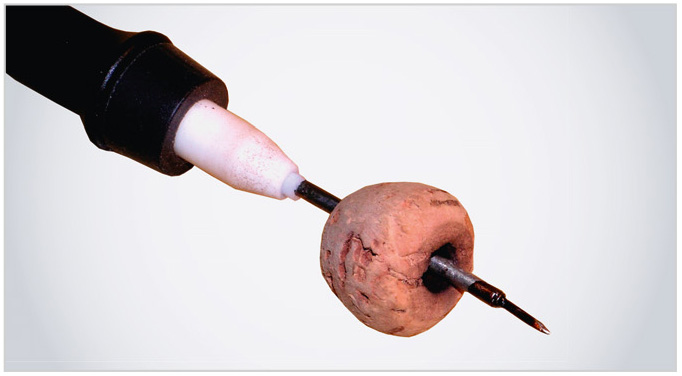
Для пайки более крупных микросхем поверхностного монтажа и электронных компонентов, таких как резисторы, конденсаторы и диоды с размерами 0805 и больше, а также для других задач, требуется мини-паяльник с немного большей мощностью. В этом случае удобно использовать автомобильный паяльник с напряжением 12 В и мощностью 8 Вт (см. рис. 38). Важно, чтобы его жало было выполнено из меди, поэтому необходимо срезать покрытие “вечного” жала до самой меди с помощью напильника.

Для питания микропаяльника (рис. 36) и мини-паяльника (рис. 38) автор приобрел источники бесперебойного питания Robiton с поэтапной регулировкой выходного напряжения в диапазоне от 3 до 12 вольт и током в 1,2 А. Этот ИБП также подвергся некоторым улучшениям. Во-первых, два отдельных диода Шоттки были заменены на более мощные, собранные в одном корпусе ТО-220. Во-вторых, для получения дополнительного напряжения в 14 В (в дополнение к 12 В) для мини-паяльника был установлен дополнительный резистор и переключатель, позволяющий изменять напряжение с 12 В на 14 В. Данные изменения сделаны для обеспечения возможности регулировки температуры жала в зависимости от размеров микросхем и прочих компонентов для поверхностного монтажа (рис. 39).
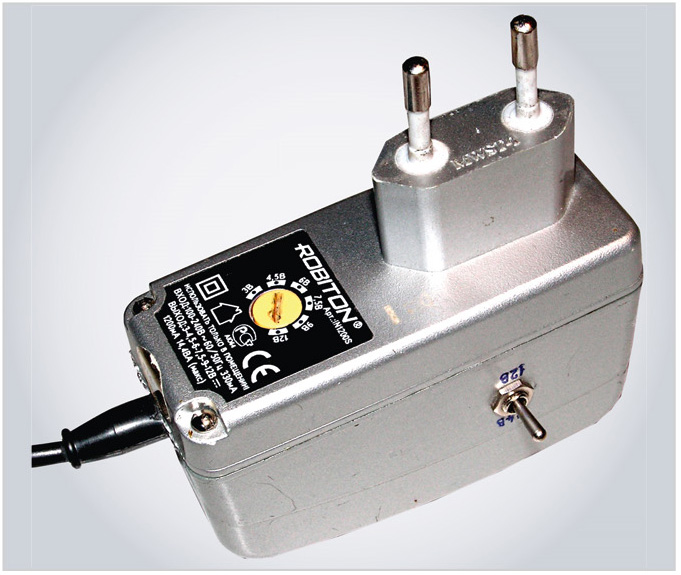
Для лужения обратной стороны печатной платы, которая в основном содержит контур земли и цепи питания, а также для обработки больших площадей на стороне платы с размещением компонентов для поверхностного монтажа требуется паяльник с мощностью около 20 Вт (см. рис. 40).

Для подготовки поверхности платы с установкой компонентов поверхностного монтажа потребуется паяльник мощностью примерно 40 Вт. Лужение можно наиболее эффективно выполнить с использованием медной лужёной оплётки, извлечённой из экранированного кабеля. Небольшой кусок этой оплётки прикрепляется к жалу паяльника при помощи медного одножильного провода с диаметром 0,5–0,6 мм, оставляя свободный конец оплётки длиной около 5–7 мм, напоминающей кисточку (см. рисунок 41).

Для распайки деталей также необходимы такие инструменты, как жидкий флюс ЛТИ-120 в бутылочке с кисточкой, припой (ПОС-61) с добавлением канифоли и зубочистки (см. рис. 42).
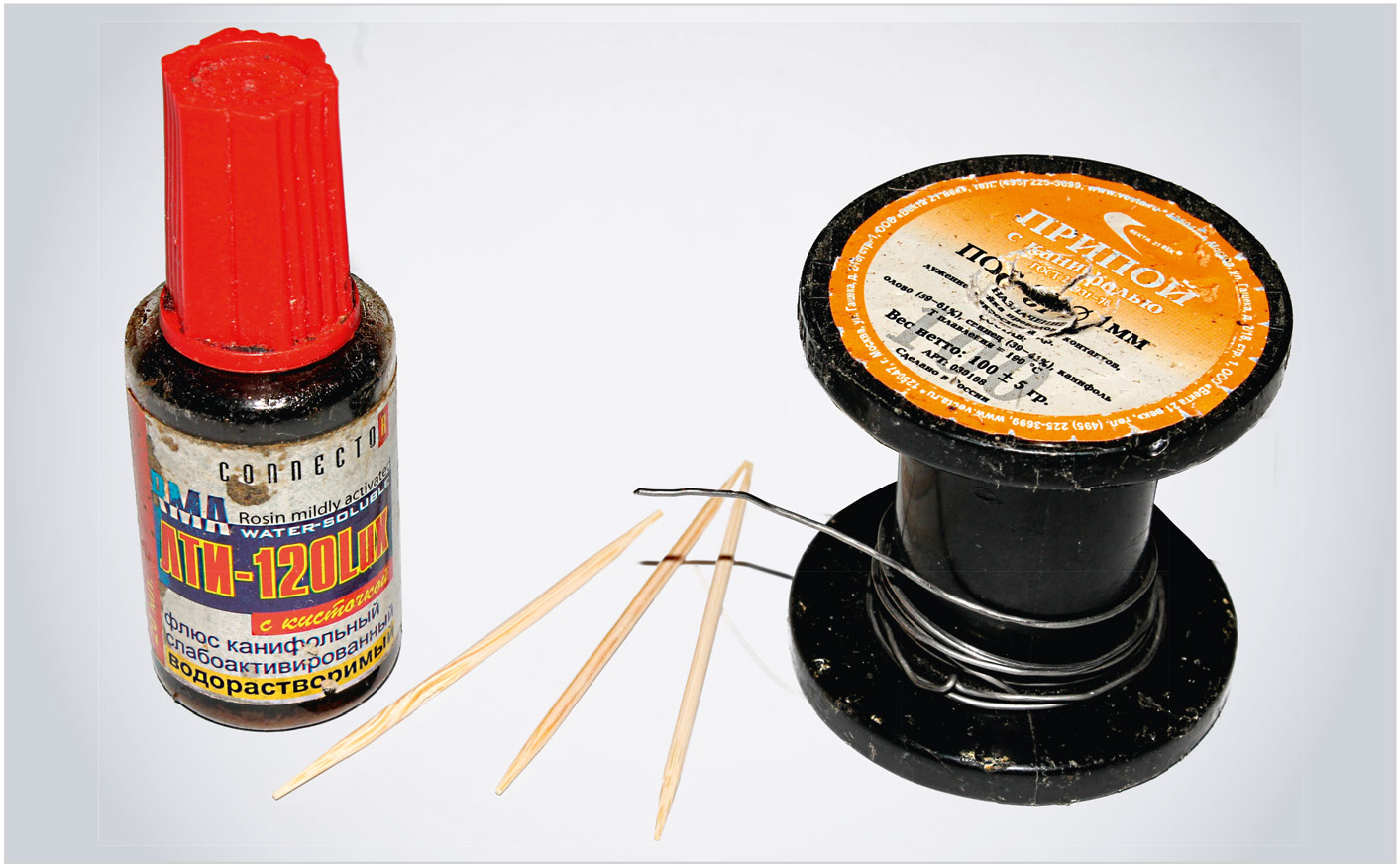
Для выполнения задачи потребуются антимагнитный пинцет с заостренными концами и игла, зафиксированная в ручных тисках, что позволит надежно удерживать небольшие предметы (рис. 43).
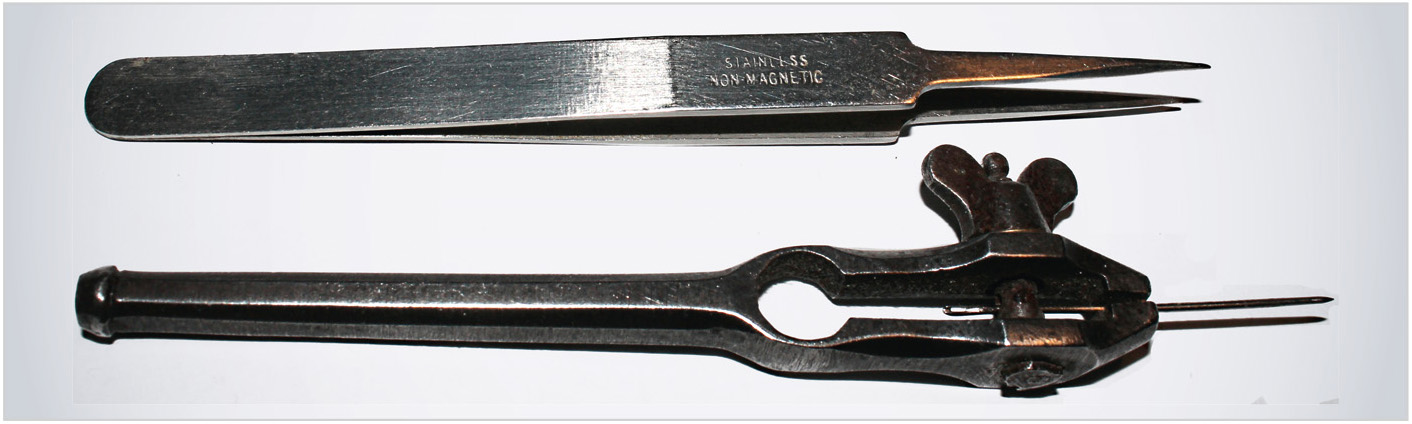
Теперь обратим внимание на процесс лужения. На взгляд автора, самым простым и качественным методом, требующим минимальных усилий и выполняемым довольно быстро, является следующий. Сначала необходимо удалить защитный лак с платы, после чего её очищают от остатков бумаги и ворса с помощью жесткой щетки из натуральной щетины и наносят флюс. Для этого плату удерживают обычным пинцетом, а при помощи кисточки, смоченной во флюсе, обрабатывают всю её поверхность. Рекомендуется осуществлять эту процедуру сразу после снятия защитного лака, чтобы избежать окисления медного покрытия. В начале процесса производится лужение оборотной стороны платы с использованием паяльника мощностью 20 Вт (см. рис. 40), после чего облуживается сторона с SMD-компонентами с помощью паяльника-кисточки (см. рис. 41). Когда паяльник прогреется, кисточку погружают в канифоль и расплавляют немного припоя, после чего проводят ею по дорожкам платы, покрывая их слоем припоя. Эта операция занимает немного времени, и результаты оказываются удовлетворительными. Благодаря мягкому ворсу кисточки даже самые тонкие дорожки (шириной до 0,2 мм) остаются неповрежденными.
Когда плата была покрыта флюсом, её следует аккуратно промыть с использованием ацетона. Теперь плата готова к процессу пайки компонентов.
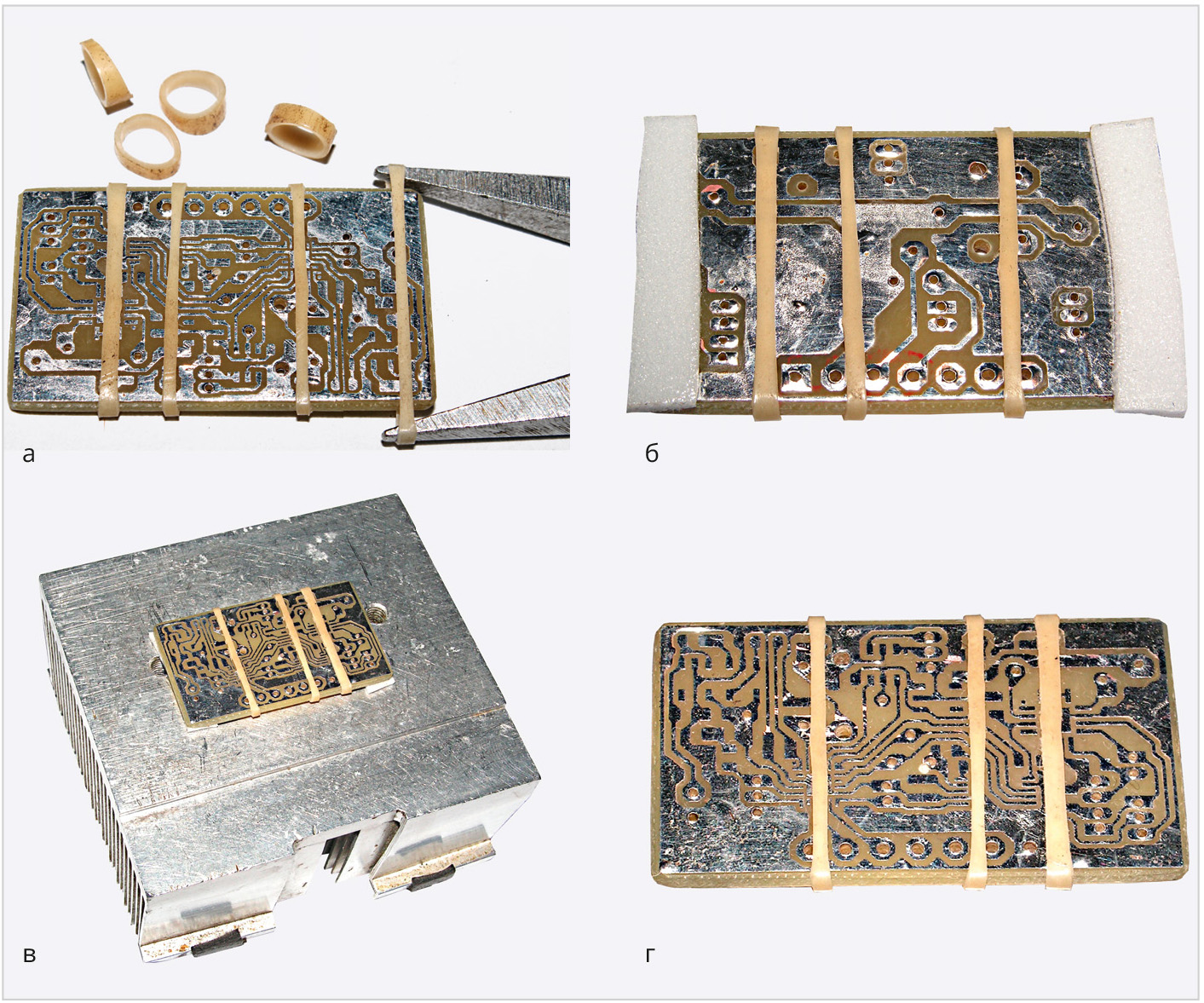
Теперь о процессе пайки компонентов. В первую очередь, с помощью узкогубцев необходимо надеть несколько растянутых кембриков на плату, которые следует предварительно подрезать ножницами (см. рис. 44а). Затем на тыльной стороне платы нужно прикрепить две полоски пористой ленты с двусторонним клеевым слоем (см. рис. 44б). После этого плату следует зафиксировать на каком-либо массивном предмете, например, на столе (в данном случае автор использовал ненужный радиатор от компьютера) – см. рис. 44в, г. После выполнения этих шагов можно начинать пайку компонентов.
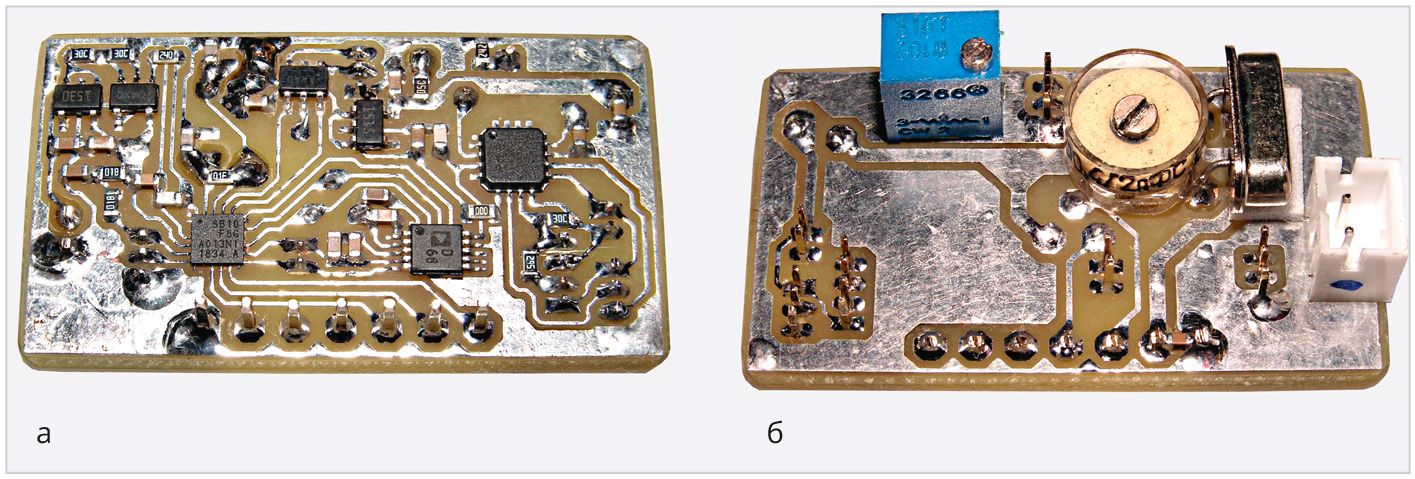
Сначала с помощью микропаяльника (рис. 36) и пинцета с острыми губками (рис. 43), а также защитных очков для пайки (рис. 10) и увеличительного стекла ×10, выполняется распайка всех SMD-компонентов. Сначала устанавливаются микросхемы и активные элементы, затем переходят к пассивным (резисторы, конденсаторы и другие). После этого всю плату обрабатывают флюсом, и мини-паяльником (рис. 38) повторно пропаиваются все активные и пассивные компоненты, за исключением микросхем с QFN-корпусами. Следующим этапом плату снимают со столика и тщательно очищают в ацетоне (рис. 45а). После этого на мини-паяльник снова устанавливаются элементы для навесного монтажа (рис. 45б). Возможно, у читателя возникнет вопрос: зачем на плату одеваются кембрики (рис. 44)? Ответ на этот вопрос будет представлен в следующем разделе статьи.
Распайка компонентов в корпусах QFN
Наибольшие сложности возникают при распайке микросхем в QFN-корпусах с очень мелким шагом, например, 0,5 мм или даже 0,4 мм. Однако это не так страшно, как может показаться. После фиксации платы с установленным кембриком на столике, с помощью иголки, которую удерживают в ручных тисках (рис. 43), осторожно захватывают и приподнимают кембрик. Затем с использованием пинцета с тонкими концами (рис. 43) помещают под кембрик микросхему в QFN-корпусе (рис. 46).
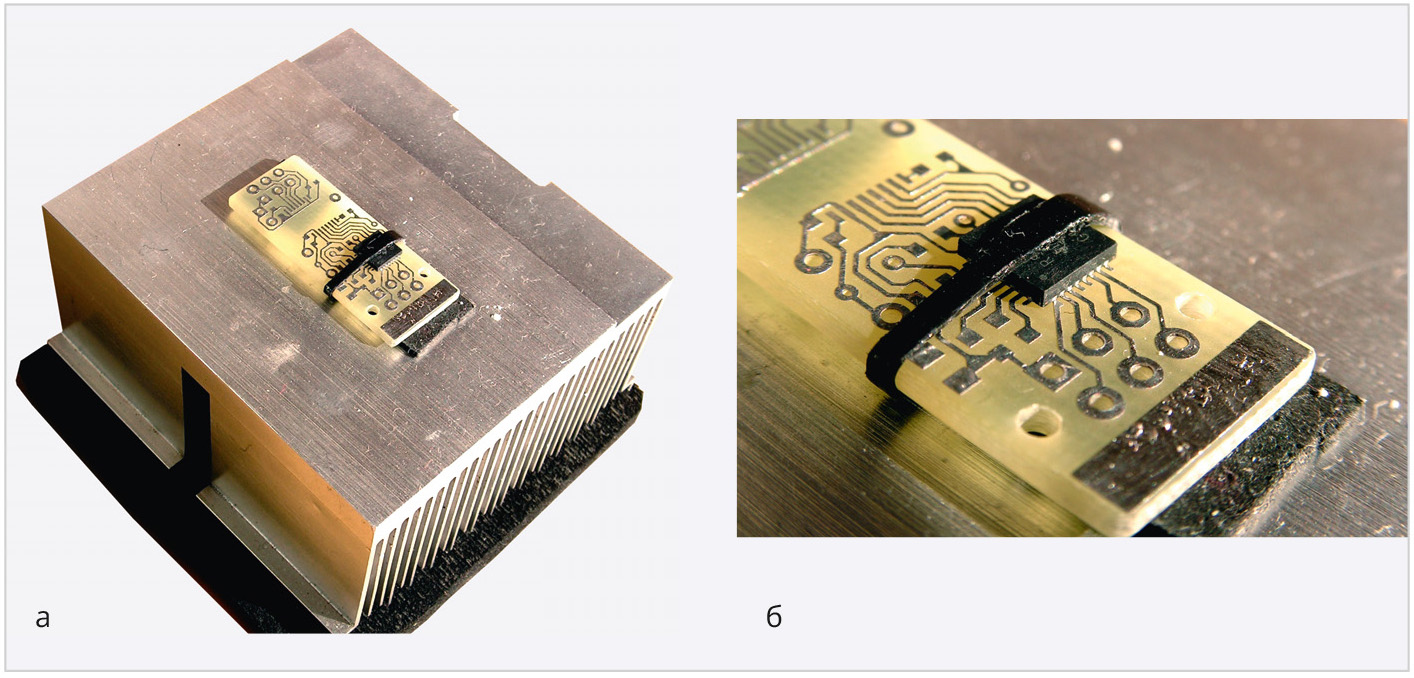
Затем, используя увеличительное стекло с увеличением ×10 и пинцет, аккуратно размещают микросхему таким образом, чтобы все контактные площадки с четырех сторон совпали с контактными площадками на печатной плате (рис. 47).

Затем, используя зубочистку, смоченную во флюсе, за нижнюю часть для предотвращения смещения микросхемы, осторожно подбираются места соединений. После этого микросхема фиксируется по углам, при этом микропаяльник дотрагивается исключительно до дорожек, избегая контакта с самой микросхемой, чтобы не вызвать её смещение (рис. 48).
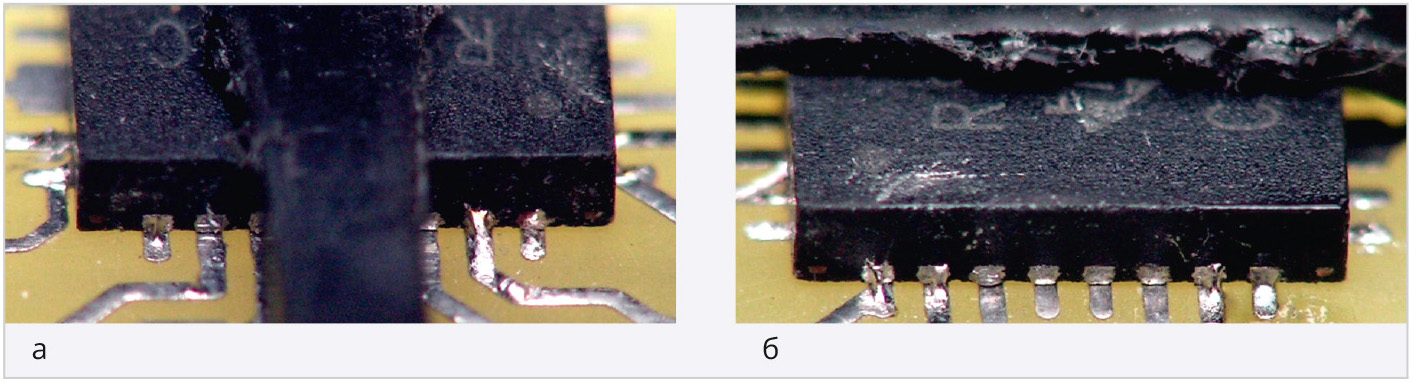
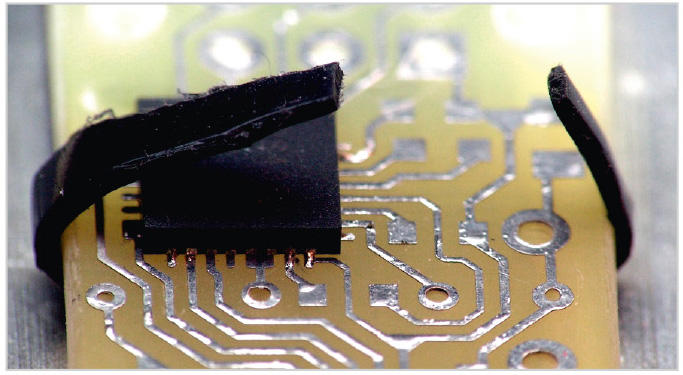
После того как микросхема установлена, клеммный шланг разрезается с помощью кусачек (рис. 49) и удаляется. Затем зубочисткой наносят флюс на все контактные площадки микросхемы и подходящие к ним дорожки с четырех сторон. После этого производится завершающая пайка всех контактных площадок микросхемы (рис. 50, рис. 51). Эти этапы также выполняются с использованием лупы с увеличением ×10.
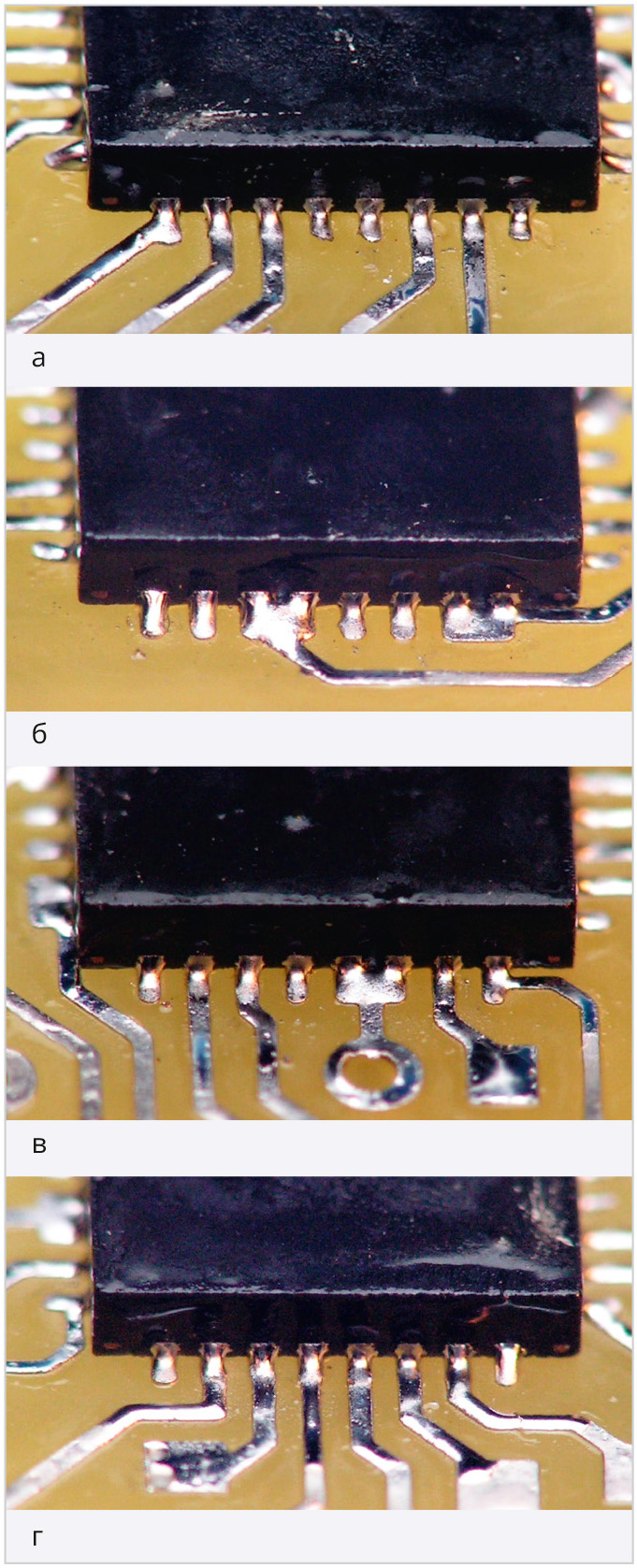
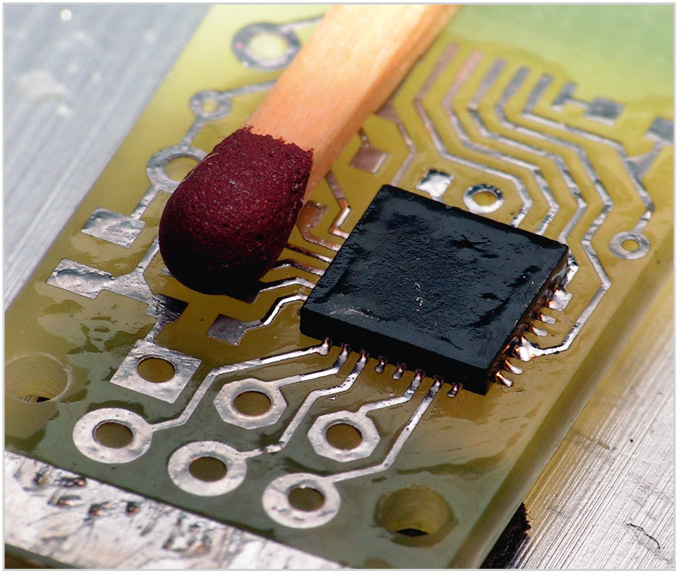
Для интегральных схем с двусторонним расположением контактов (см. рис. 52) требуется применение кембрика для точного их размещения. В связи с этим на плате должно быть несколько таких элементов (см. рис. 44) – это и является ответом на вышеозначенный вопрос.
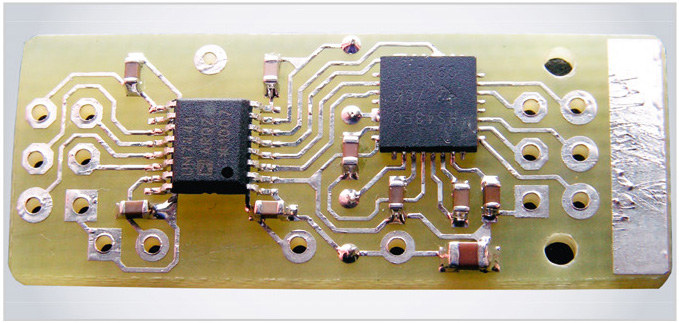
Иллюстрации процесс распайки чипов в корпусах типа QFN (см. рис. 53) наглядно демонстрируют, что описанная выше технология пайки довольно проста, а микросхемы надежно соединены с платой. В этом нет ничего особенно сложного.
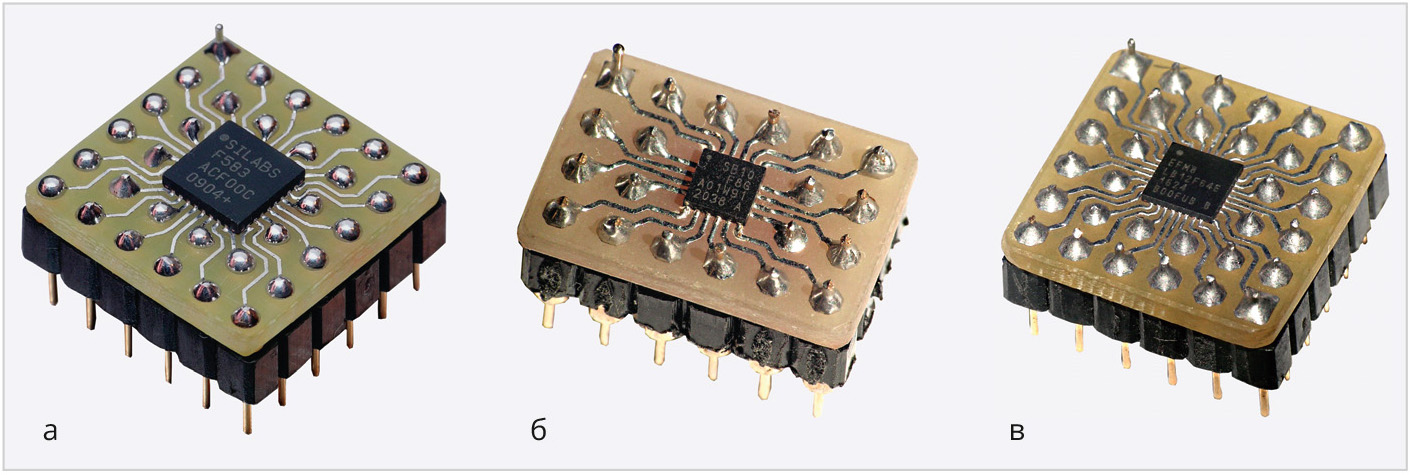
Выпаиваем микросхемы и компоненты в «неудобных» корпусах
Порой необходимо извлечь микросхему из платы, выполненной с использованием технологии поверхностного монтажа (SMD). Если выпаивать микросхемы с двусторонними выводами (например, SOIC, SSOP) не составляет большого труда, то сложность возникает с квадратными микросхемами, которые имеют выводы на всех четырёх сторонах, такими как QFP и особенно безногие QFN, у которых выводы представлены в виде контактных площадок на боковых гранях. Дополнительную сложность усугубляет наличие заземляющей пластины внутри QFN, которая тоже припаивается к плате. Обычно для их выпаивания применяются достаточно дорогие выпаечные фены, стоимость которых начинается от 2000 рублей. Их горячий воздух плавит припой, позволяя удалить микросхему. Однако у этого метода есть два существенных недостатка: высокая цена инструмента и риск повреждения самой микросхемы при нагреве до температур плавления припоя, что особенно критично для микроконтроллеров с предустановленным программным обеспечением. Альтернативный способ нагрева обратной стороны платы требует столь интенсивного тепла, что может привести к повреждению самой платы.
Представляем альтернативный метод нагрева обратной поверхности печатной платы с использованием инфракрасного излучения от галогенной лампы. В этом процессе обратная сторона платы не подвержена угару и практически не нагревается, в то время как припой на стороне микросхемы разогревается до такой меры, что микросхема легко удаляется с платы. Цена такой галогенной лампы значительно ниже стоимости фена, порой в десятки раз, а конструкция подобного “нагревателя” отличается простотой, что также делает его доступным по цене. В дальнейшем будет подробно рассмотрена конструкция этого устройства, объяснены принципы его работы и приведены результаты использования.
Для создания устройства автор выбрал галогенные лампы с керамическим цоколем, который способен выдерживать высокие температуры, и соответствующие для них патроны. Эти лампы обычно применяются в осветительных прожекторах, которые могут функционировать в течение длительного времени без перерывов. Данные галогенные источники света работают от сетевого напряжения около 220 В и имеют цоколь R7s, дополненный керамическими изоляторами. Наименее длинные из представленных ламп имеют размеры 78 мм (см. рисунок 54).
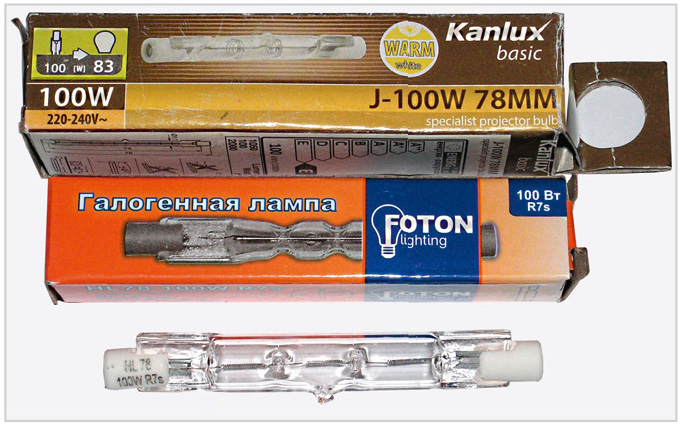
Для этих ламп существуют специальные патроны, изоляторы которых также изготовлены из фарфора. Примером может служить патрон LH39 (230V R7s J78), который способен выдерживать максимальную мощность до 1500 Вт! Такой патрон дополнительно оборудован специальными проводами, устойчивыми к высоким температурам, длиной примерно 20 см. Эти провода имеют двойную изоляцию: внутренний проводник обернут лентой из фторопласта, а снаружи располагается дополнительный изолирующий слой из термостойкой стеклоткани.
Лампы и патроны к ним стоят не больше 50 рублей за штуку. Лампы с цоколем R7s длиной 78 мм легко найти, так как они широко доступны. Однако цоколь LH39 для них, по какой-то причине, встречается реже. Тем не менее, автору удалось его отыскать. Если же не удастся найти нужный вариант, его можно купить на онлайн-торговой площадке, но цена будет значительно выше — примерно от 200 до 250 рублей.
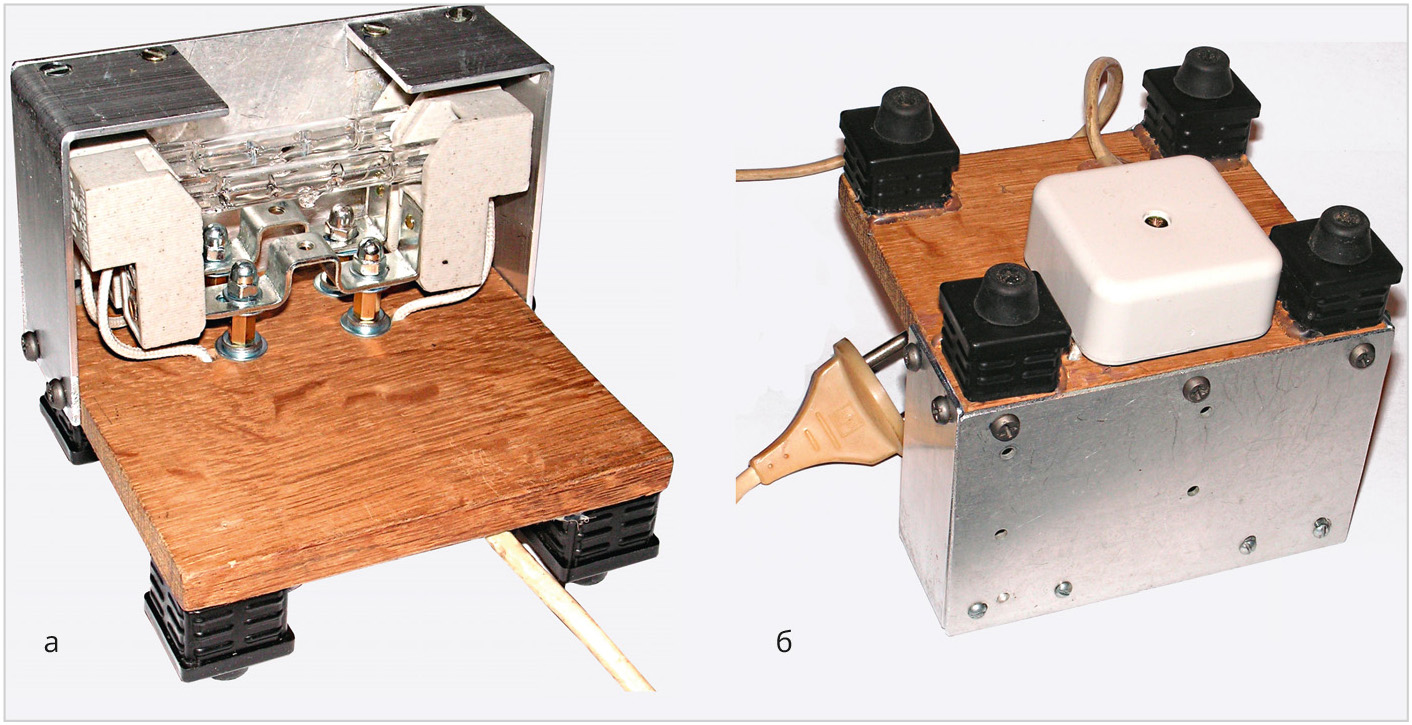
На основе этих ламп и их патронов было разработано устройство для выпаивания микросхем. В качестве основы конструкции (рис. 55) использовалась дубовая доска, обработанная с помощью строгального станка, шириной 10 см и толщиной 1 см. От нее был отрезан фрагмент длиной 11 см. Для крепления патронов двух ламп применены две шестигранные латунные стойки длиной 10 мм, одна сторона которых оснащена шпильками с резьбой М4, а другая — внутренней резьбой М4. Стойки надежно закреплены на доске с помощью винтов М4, ввинченных через предварительно просверленные отверстия. Патроны фиксируются на стойках двумя гайками М4 и стандартными шайбами. Провода были пропущены через отверстия в доске (рис. 55а) и соединены с сетевым кабелем на обратной стороне — обе лампы работают в параллельном соединении. Ввиду упрощения конструкционного описания схема не представлена. Соединения выполнены в распределительной коробке, прикрепленной к доске двумя саморезами (она изображена белого цвета на рис. 55б). Сетевой кабель дополнительно прикреплен к поверхности доски с помощью термоклея. Чтобы предотвратить скольжение устройства, в уголках доски установлены пластиковые мебельные подпятники, которые, вместе с резиновыми ножками, прикручены саморезами и дополнительно закреплены термоклеем для устойчивости (см. рис. 55б). Чтобы избежать случайного контакта с токоведущими контактами патронов и предотвратить ослепление от света ламп, с обеих сторон доски закреплены по два уголка из алюминиевой полосы шириной 35 мм и толщиной 2 мм, согнутых под углом 90°, с использованием двух саморезов. К этим уголкам прикреплена алюминиевая пластина, с помощью ещё двух уголков размером 10×10 мм и толщиной 1,5 мм, в которых просверлены отверстия и нарезана резьба М3, с использованием винтов М3. Кроме того, алюминиевая пластина дополнительно прикручена к доске через саморезы с нижней стороны. Данная конструкция обладает достаточной жесткостью, что позволяет избежать деформации под воздействием высоких температур. Опыт эксплуатации устройства показал, что даже пластина и уголки не становятся горячими, и их можно без опаски трогать рукой. По ощущениям автора, при работе ламп в течение 5 минут температура алюминиевого кожуха не превышала 40°C. Далее устройство оставалось включенным в течение получаса. За это время с ним не произошло никаких изменений, хотя кожух немного нагрелся, но не до такой степени, чтобы стало невозможно его касаться (примерно до 50°C).
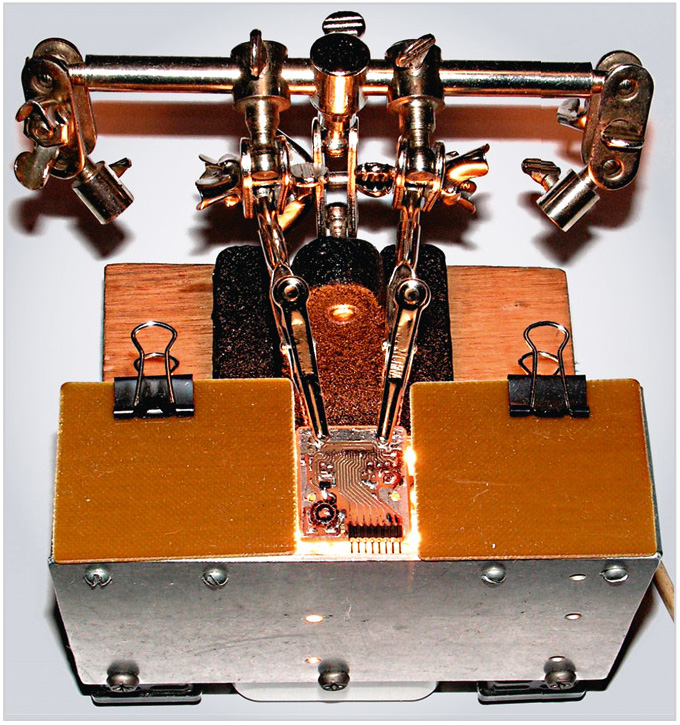
На освободившемся участке доски установлено известное устройство, называемое «третья рука», которое долгое время не использовалось. Оно оснащено двумя зажимами типа «крокодил», обеспечивающими надежное крепление платы с удаляемой микросхемой на расстоянии примерно 20 мм от ламп (см. рис. 56). Чтобы избежать ослепляющего света от ламп, по обеим сторонам платы были установлены шторки из тонкого одностороннего стеклотекстолита толщиной 1 мм, прижимаемые к уголкам корпуса с помощью двух канцелярских зажимов медной стороной вниз. Расстояние между шторками можно легко изменять в зависимости от размера платы. Через 3–4 минуты нагрева микросхему можно будет аккуратно удалить с помощью стандартного тонкого пинцета. При этом плата не выделяет никаких посторонних запахов, так как не перегревается, но благодаря инфракрасному излучению ламп, проникающему через плату и нагревающему дорожки, припой плавится весьма эффективно.
Автор проводил исследования по работе устройства с использованием ламп различной мощности: 60, 100 и 150 Вт. Результаты эксперимента показали, что при применении 60-ваттных ламп, даже при 10-минутном прогреве на расстоянии 20 мм от платы, припой не плавится, что делает использование таких ламп нецелесообразным. В случаях с лампами мощностью 150 Вт, уже через 2 минуты нагрева плата начинает перегреваться, что приводит к появлению дыма и неприятного запаха. Кроме того, такие лампы очень яркие и могут вызывать дискомфорт для глаз. Использование 100-ваттных ламп, напротив, обеспечивает идеальную работу устройства: для успешного выпаивания компонентов достаточно всего 3-4 минут прогрева, и в этом процессе не возникает никаких резких запахов от платы.
Следует отметить, что есть некоторые аспекты, касающиеся эксплуатации данного устройства. Прежде всего, даже при использовании 100-ваттных ламп могут возникнуть ситуации, когда мощность следует немного уменьшить. Если необходимо удалить значительное количество элементов с платы, например, десяток конденсаторов, несколько резисторов или диодов, а также более простые микросхемы, то процесс разогрева припоя займет определенное время (несколько минут). В течение этого времени сильный нагрев может вызвать дымление платы и появление неприятного запаха. Чтобы избежать подобных ситуаций, рекомендуется снизить уровень нагрева.
Во-вторых, для эффективного использования ламп с мощностью 150 Вт необходимо также ограничить их отопительную интенсивность, как было упомянуто ранее.
В-третьих, при включении ламп, когда их нити накаливания еще не прогреты и обладают низким сопротивлением, начальный ток может значительно увеличиваться, что таит риск повреждения ламп — они могут просто перегореть, что довольно часто происходит с лампами накаливания. Поэтому важно ограничивать мощность ламп в момент их включения.
Эти три проблемы можно легко решить с помощью простого симисторного регулятора мощности, который будет описан далее.
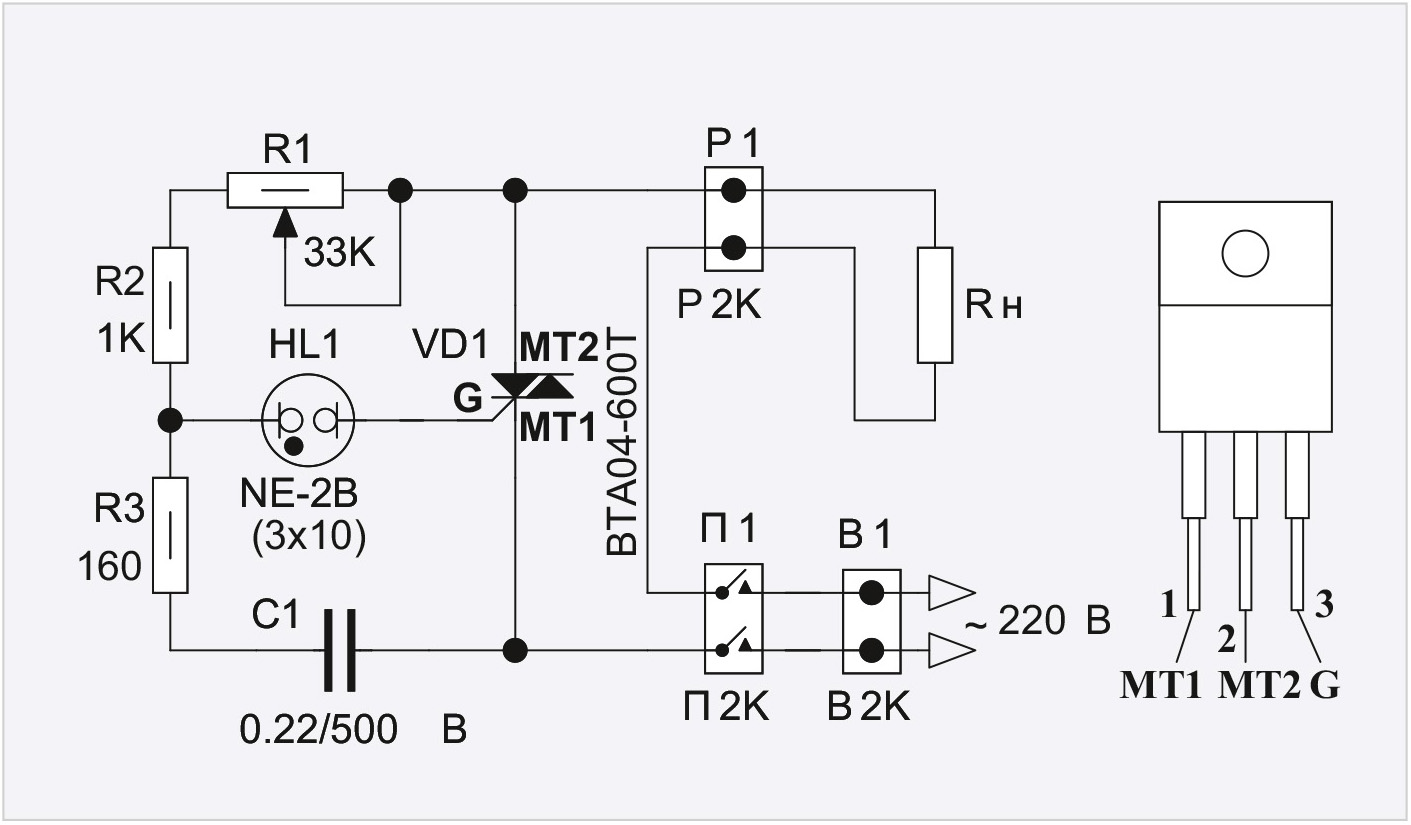
Основание для схемы регулятора мощности, представленной на рисунке 57, было взято из давней работы автора [7], в которой используется симистор MAC97A8 в корпусе ТО-92 с предельным током 1 А и током включения (IGT) 5 мА, поступающим на управляющий электрод (G). Уникальной чертой данной схемы является применение миниатюрной неоновой лампы NE-2B с голубым свечением, размеры которой составляют всего 4×9 мм, для управления симистором вместо динистора, как это делается в хорошо известных аналогичных устройствах. Неоновая лампа имеет три ключевых преимущества по сравнению с динистором. Во-первых, два электрода неоновой лампы изолированы друг от друга, что препятствует проникновению помех от сетевого напряжения, возникающих при переключениях симистора, на ее управляющий электрод. Во-вторых, довольно малый ток, протекающий через лампу (пара миллиампер), при включении неона, с одной стороны, остаётся ниже предельного значения тока управляющего электродом симистора, а с другой – вполне достаточен для его активации. Эти два фактора защищают симистор от повреждений, то есть предотвращают его перегрев из-за высокого тока на управляющем электроде, что значительно улучшает надёжность работы регулятора. В-третьих, неоновая лампа служит своеобразным индикатором, по её яркости можно оценить мощность, которую пропускает симистор. Однако в данном случае наблюдается обратная зависимость – чем меньше светится лампа, тем выше мощность, проходящая через симистор.
Как показывает схема на рис. 57, в ней используется симистор BTA04-600T (VD1), который представлен в корпусе ТО-220. Он имеет максимальное напряжение 600 В, максимальный ток в 4 А и порог срабатывания IGT равный 5 мА, что аналогично характеристикам MAC97A8, что делает управление устройством возможным с помощью неоновой лампы. Однако при работе с максимальной нагрузкой, когда галогенные лампы функционируют на полную мощность, симистор испытывает значительный ток, что ведет к его нагреву. Поэтому для его стабильной работы необходим небольшой радиатор. В данном случае автор использует алюминиевое дно корпуса, к которому крепится симистор.
Необходимо сделать краткое замечание о типах корпусов симисторов. Симисторы, рассчитанные на максимальный ток в 4 А и выше, производятся в двух основных вариантах корпусов. Первый вариант — это традиционный корпус TO-220 с металлической основой, которая имеет отверстие для крепления на радиаторе. Металлическая основа может быть либо в контакте с центральным электродом симистора (MT2), либо изолирована от него. Второй вариант — это полностью изолированный пластиковый корпус SOT186A (TO-220F), также имеющий отверстие для прикрепления к радиатору. Чтобы исключить случайное соприкосновение с сетевым напряжением, если рукой затронуть дно корпуса, оно должно быть защищено от этого высокого напряжения. Если симистор в корпусе TO-220 имеет металлическое основание, которое контактирует с центральным электродом, для обеспечения изоляции днища от высоких напряжений необходимо использовать изоляционную прокладку, предпочтительно керамическую, и специализированную изоляционную втулку. Однако цена керамической прокладки значительно высока и может достигать стоимости самого симистора, что делает такой способ изоляции нежелательным. Теплопроводность металлического основания корпуса TO-220 несколько выше, чем у пластмассового корпуса SOT186A. В связи с этим наиболее целесообразным вариантом является использование симисторов в корпусе TO-220 с изолированным металлическим основанием.
Для обеспечения управления симистором с помощью низкого тока неоновой лампы NE-2B (HL1) ток управления не должен превышать 5 мА. Эти симисторы также известны как симисторы с логическим уровнем управления (Logic Level Triac).
Итак, наиболее разумно использовать симисторы в корпусе ТО-220 с изолированным металлическим основанием и с управлением логическим уровнем. Одним из таких симисторов является BTA04-600T (VD1), который использован в схеме, представленной на рис. 57. Также положительные результаты продемонстрировал симистор BTA208X-1000C, имеющий полностью изолированный пластиковый корпус SOT186A.
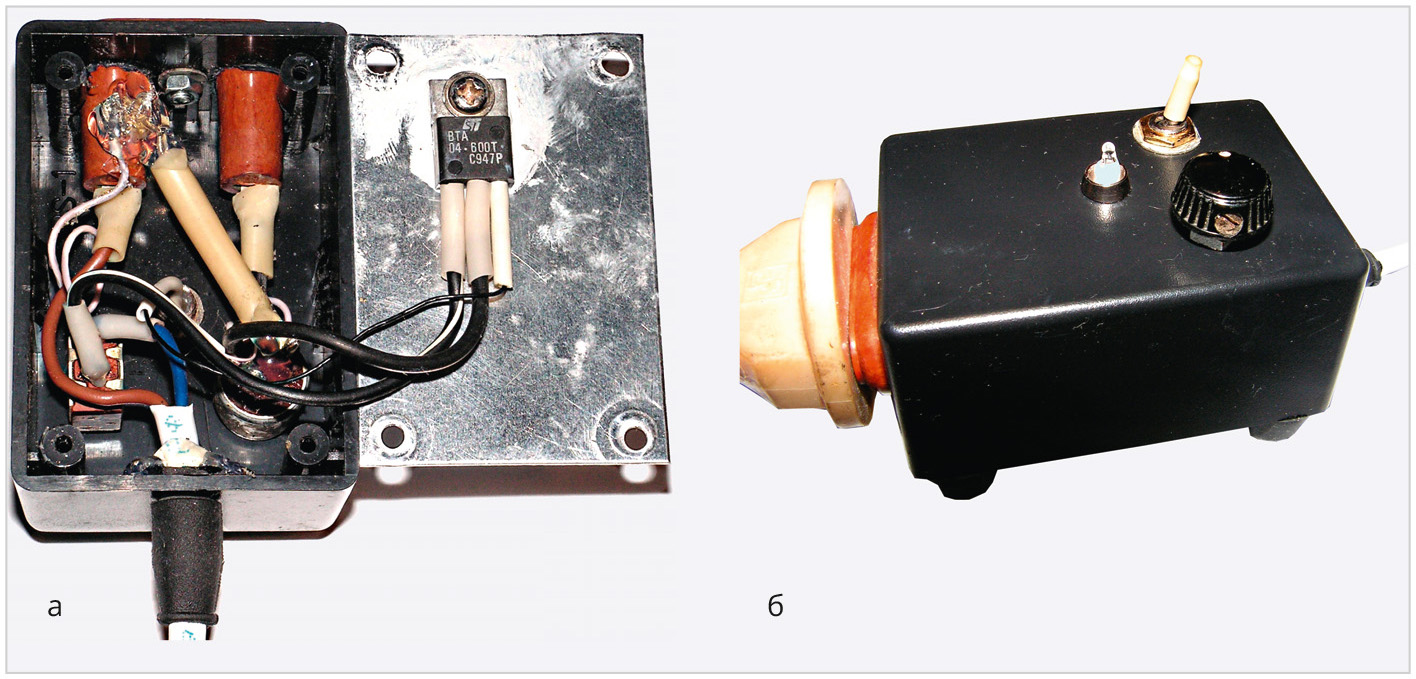
Теперь рассмотрим конструкцию регулятора. Он выполнен в пластиковом корпусе G1031BA размером 64×44×30 мм, с основанием из алюминия (см. рис. 58). На узкой боковой стороне корпуса расположена розетка Р1 (РД1-1, с номинальным током 6 А) из карболита, в которую вставляется вилка от устройства с галогенными лампами (обозначенная на схеме рис. 57 как Rн). Она прикреплена к корпусу с помощью винта М3 с потайной головкой и гайки. На верхней поверхности корпуса с соответствующими гайками закреплены переменный резистор R1 (СП4 1 – 0,5 Вт) с ручкой на штоке и выключатель П1 (П1Т-1-1В, рассчитанный на 5 А). Лампочка (NE-2B размером 4×9 мм) помещена в металлический держатель для светодиодов (RLL-3010), который также прикреплён к верхней части корпуса с помощью гайки. Внутренний диаметр резьбовой трубки держателя составляет 4,2 мм, что позволяет легко вставить лампу, а конусная полиэтиленовая заглушка (в комплекте с держателем) надежно фиксирует её на месте. Керамический конденсатор поверхностного монтажа с размером 2220 (5,6×5×1,8 мм) закреплён с помощью термоклея на одном из выступов розетки. К одному из контактов припаян резистор R3 (см. рис. 57), а к переменному резистору подключён резистор R2. Эти два резистора соединены между собой и покрыты кембриком (ПВХ-трубка), который разрезан вдоль и надёжно зафиксирован термоклеем с обеих сторон. Сетевой кабель с вилкой В1 проходит через резиновую втулку, установленную на второй узкой боковой стороне корпуса, и дополнительно фиксируется термоклеем. Симистор VD1 монтируется на внутренней поверхности дна корпуса с помощью винта М3 и гайки, применяя теплопроводную пасту КПТ-8. Благодаря тому, что все элементы закреплены непосредственно на корпусе, печатная плата не требуется, а все соединения выполнены проволокой с сечением не менее 0,5–0,8 мм², кроме проводов для неоновой лампы, которые имеют сечение 0,05–0,1 мм². Для предотвращения скольжения корпус оборудован четырьмя резиновыми ножками на дне.
Автор исследовал функционирование устройства с лампами мощностью 150 Вт. Чтобы обеспечить приемлемый уровень нагрева печатной платы, ручка резистора регулировки мощности должна быть установлена примерно на две трети от своего максимального вращения, что соответствует около 200° (максимальный угол поворота резистора СП4 1 составляет 300°).
При использовании ламп мощностью 100 Вт угол их наклона должен быть максимальным. Выходное напряжение этого регулятора приблизительно на 10 В ниже входного. Так, если входное напряжение составляет 220 В, то максимальное выходное напряжение ограничивается 210 В. Когда ручка переменного резистора полностью прислонена влево, минимальное напряжение составляет около 35 В. Измерение напряжений осуществлялось с помощью стрелочного тестера (ТЛ-4) в диапазоне «~300 В» для определения действующего значения переменного напряжения.
Дополнительно стоит отметить, что регулятор, оснащенный симистором, рассчитанным на ток в 4 А, можно применять не только в случае с обогревателями, но и с другими устройствами для нагрева, такими как паяльники и электроплитки, мощность которых не превышает 800 Вт. Если использовать симистор с пределом тока в 8 А, то мощность подключаемых нагревательных приборов может достигнуть 1,5 кВт.
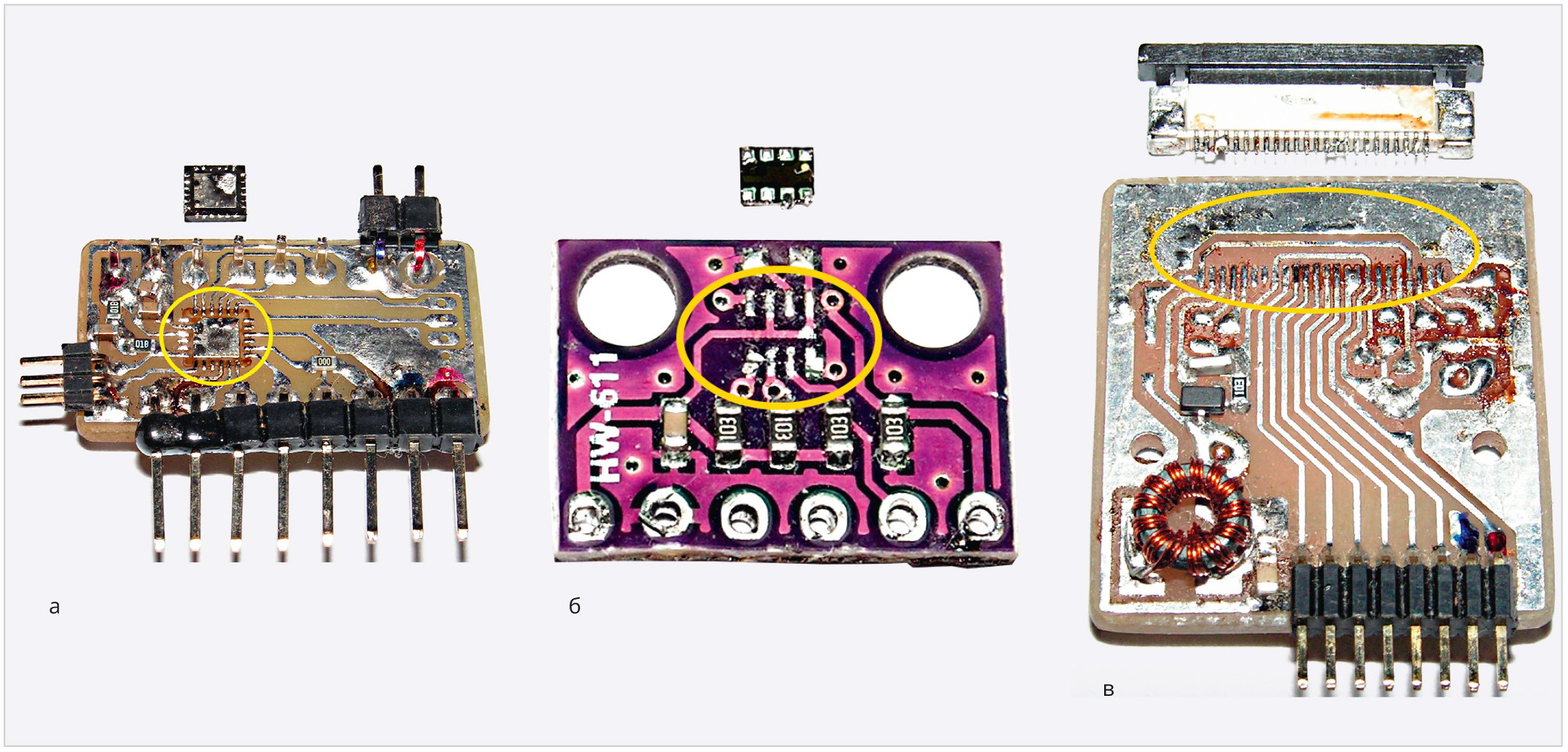
Примеры работы устройства (см. рис. 59) наглядно показывают, что с его использованием можно не только легко выпаять микросхему формата QFN-24 (рис. 59а), но также удается успешно выпаивать микросхемы формата LGA-8 (рис. 59б). У таких микросхем выводы находятся на нижней стороне, и они находятся на значительном расстоянии от краёв корпусов, что делает невозможным их прогрев обычным паяльником без риска повреждения самой микросхемы. Кроме того, при необходимости выпаять 24-контактный разъём для подключения шлейфа, у которого контакты и крепёжные площадки на боках припаяны к плате (рис. 59в), необходимо одновременно прогревать каждый контакт и крепёжную площадку. Сделать это даже с двумя паяльниками окажется сложным.
С использованием описанного устройства, после предварительного нагрева платы, все элементы (см. рис. 59) можно легко извлечь пинцетом.
Как видно на рис. 59, все демонтированные компоненты имеют заусенцы из остатков припоя, и некоторые контакты разъёма даже соединены между собой (см. рис. 59в), что делает их непригодными для повторного использования. Для решения этой проблемы необходимо удалить все остатки припоя с компонентов.
Чтобы выполнить эту задачу, необходимо прикрепить компонент к маленькому участку пористой ленты с двусторонним клеящим слоем, который расположен на столике (см. рис. 44в, рис. 46а). Затем следует нанести жидкий флюс на компонент (например, микросхему или контакты разъёма) с помощью кисточки (см. рис. 42).
Затем к насадке мини-паяльника (см. рис. 38) необходимо привязать тонким одножильным проводом диаметром 0,2–0,3 мм примерно 30–40 тончайших (0,05–0,1 мм в диаметре) медных нитей с покрытием из серебра. Эти нити можно извлечь, например, из провода типа МС16-13 сечением 0,03–0,05 мм². Перед тем как привязать нити к насадке, их следует аккуратно скрутить, а после привязывания расправить так, чтобы получилась некая форма насадки-кисточки (см. рис. 60). Далее, используя такую насадку на мини-паяльнике и под лупой с увеличением ×10, нужно осторожно удалить все заусенцы с соответствующего элемента.
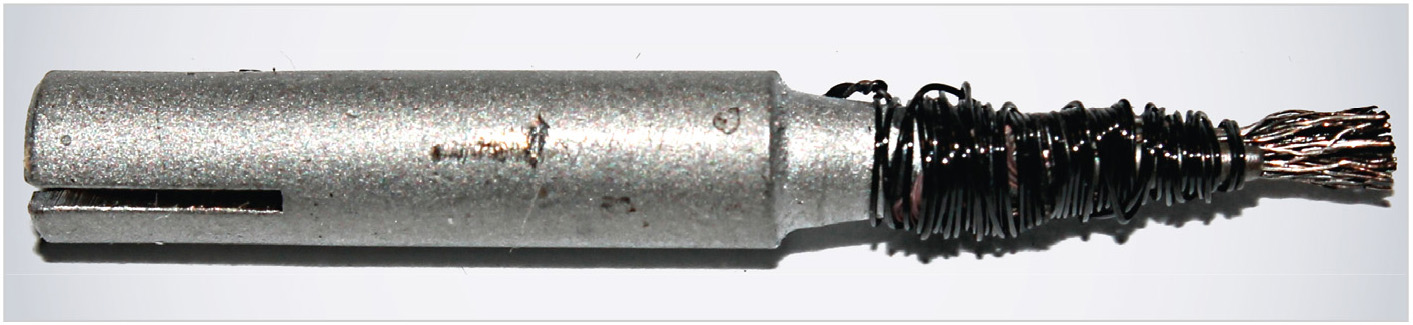
По завершении тщательной очистки элемента в ацетоне, он становится пригодным для последующего применения. Автор провел тестирование функционирования программы микроконтроллера, извлеченного аналогичным способом. Результаты проверки подтвердили, что программа сохранила свою работоспособность.
Заключение
В завершение следует подчеркнуть несколько моментов. Несмотря на то что статья в некотором роде имеет производственное направление, её главная аудитория – это разработчики электронных устройств, а не производители печатных плат. Автор прекрасно понимает на собственном опыте, как много усилий, времени и ресурсов затрачивает разработчик, чтобы получить печатную плату через стороннюю компанию. Сколько времени уходит на многократную проверку схемы и исправление ошибок, допущенных проектировщиком. Кроме того, ошибки, сделанные разработчиком, автоматически передаются на схемы и, в конечном итоге, на саму плату. В лучшем случае такие ошибки можно исправить, подрезав дорожки и добавив новые соединения, но в худшем случае потребуется заказывать новую плату, что обернётся дополнительными затратами, как финансовыми, так и временными.
Если разработчик самостоятельно создает печатную плату, пусть даже это не так аккуратно выполнено по сравнению с работой профессионала в плане разводки и сверления, то самое серьезное, что ему может грозить за свои просчеты, – это легкий шлепок по лбу. Зато такая работа не требует затрат денег. Именно для этого и предназначена данная статья.
Литература
- Кузьминов А. Метод фоторепродуцирования для изготовления фотошаблона печатных плат в домашних условиях // Технологии в электронной промышленности. 2010. № 5. С. 17–23; № 6. С. 10–15; № 7. С. 8–15.
- Кузьминов А. Изготовление устройств на печатных платах с высоким разрешением в домашних условиях // Технологии в электронной промышленности. 2010. № 8. С. 18–25; 2011. № 1. С. 9–13; № 2. С. 18–25.
- Кузьминов А. Технология изготовления печатных плат с высоким разрешением в домашних условиях // Радио. 2017. № 10. С. 24–28.
- Кузьминов А. Как использовать фольгу односторонней печатной платы в качестве общего провода // Радио. 2019. № 2. С. 28–30.
- Кузьминов А. Тиристорный регулятор скорости вращения коллекторных двигателей постоянного тока // Современная электроника. 2013. № 2. С. 50–53.
- Кузьминов А. Усовершенствованное устройство для выпаивания микросхем в корпусах QFN/QFP // Радиолоцман. 2023. № 3–4. С. 60–66.
- Кузьминов А. Регулятор мощности паяльника в сетевой вилке // Современная электроника. 2014. № 2. С. 48–49.